TIRE
Small chemicals weighing system
Automatic Dosing System for Small Chemicals weighing for the production of tires. Recipes are automatically bagged, unbagged and delivered to customer’s mixer without human intervention.
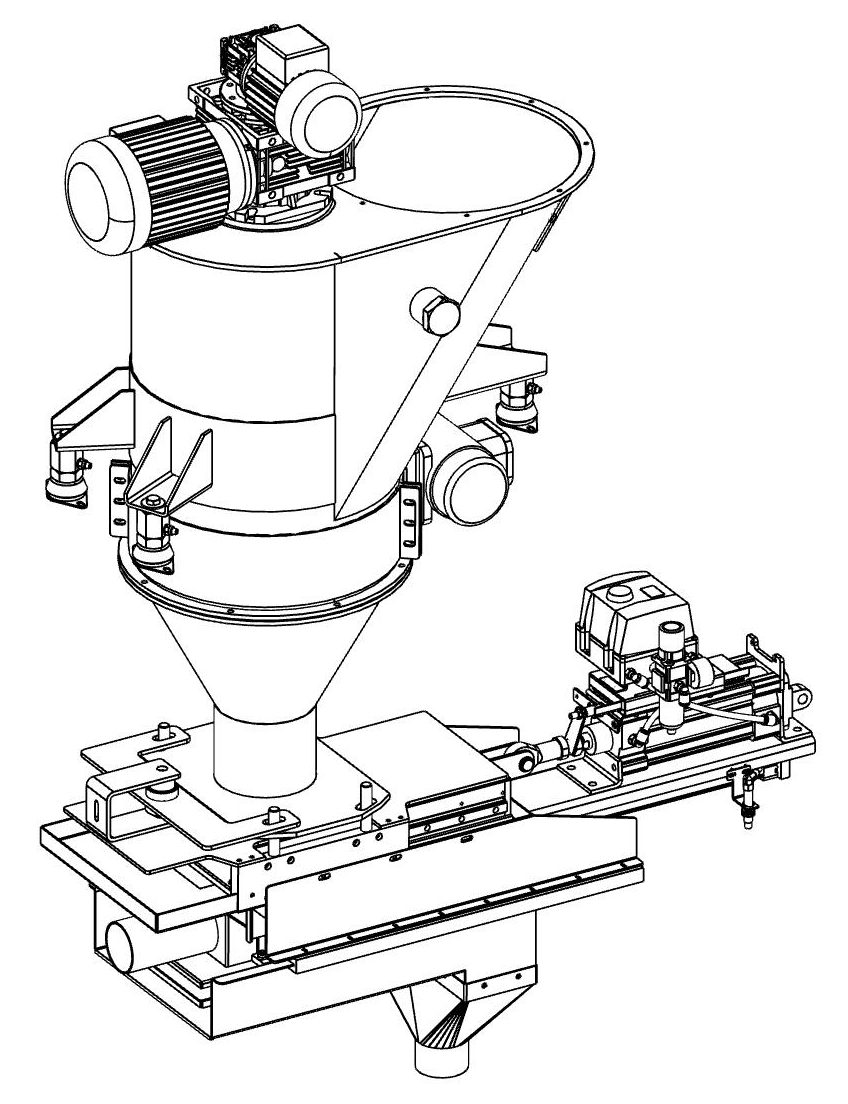
Tire
The reason to invest in an automatic dosing system:
Accuracy
Traceability
Atex Compliance
Reliability
User-Friendly
Anti-dust device fitted with self-cleaning filter during the dosing phase in order to avoid the spread of dust in the working environment.
Protection of the plant environment and the employees. Reduction in staff needed: operator activity is limited just for the loading of products.
The system is modular and compact. In case of future requirements, it is possible to add modules to increase the number of products to be managed.
Increased accuracy in the weighing, thanks to a certified weighing system.
High speed dosing thanks to the contemporary weighing of all components.
Creation and automatic management of bag with labelling of identification data.
Management software program designed and accomplished by sector experts.
Traceability of the dosing in real time.
Elimination of waste and human error.
High safety standard in accordance to current regulations.
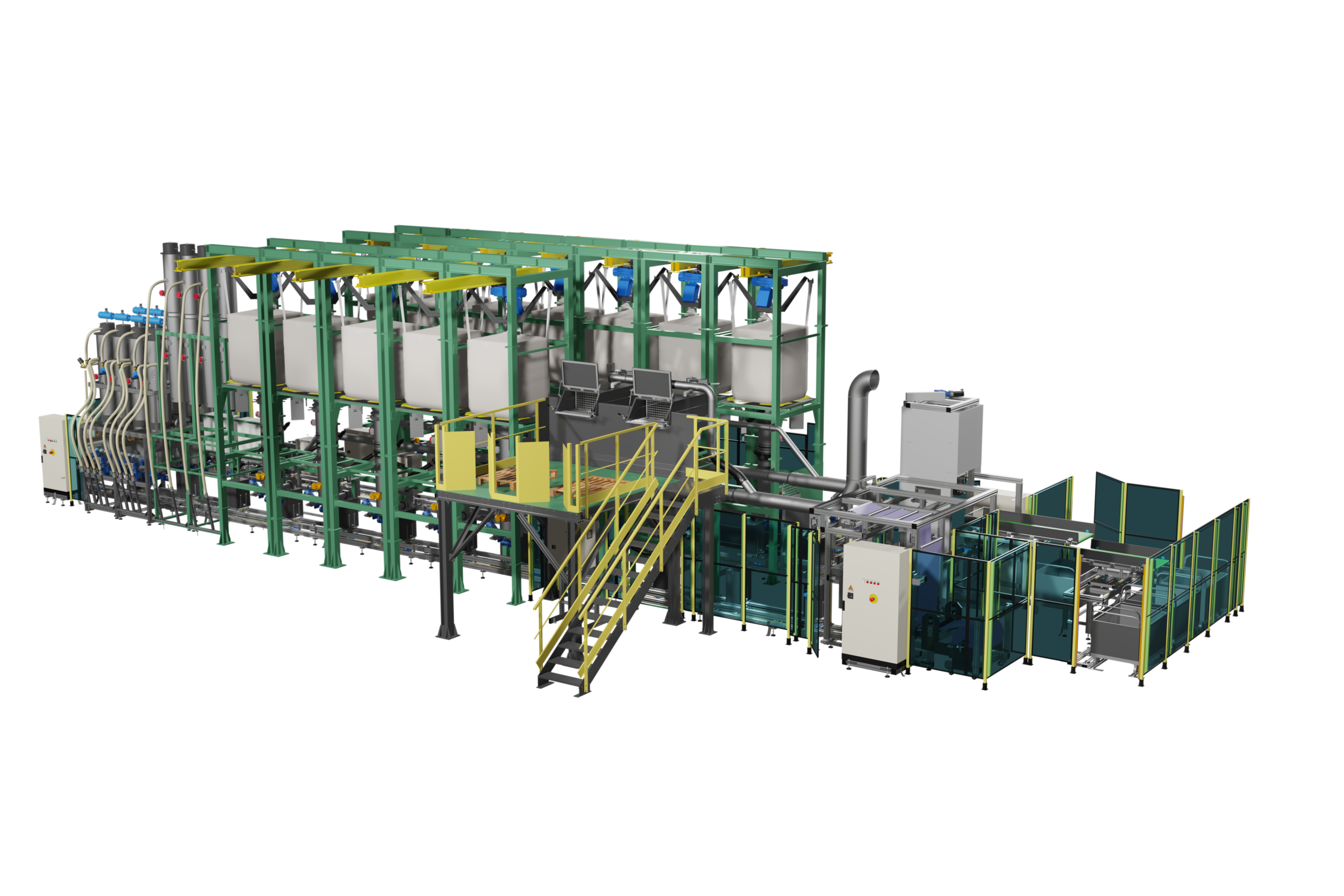
Small chemicals dosing system for tire compounds manufacturers
Raw materials can be stored in silos, supplied in Big-Bags, containers, or introduced as bulk material via feeding hoppers and subjected to barcode identification. This versatility accommodates different types of ingredients.
Silos could be equipped with mechanical bridge breakers for a better flow of conglomerated products. All the patented Color Service system carry the mark “CE”. They will therefore be in accordance with the present safety regulations and particularly with the European norm n. 2006/42/EC named “CEE machine directives”.
The production cycle
01
Creation of the bag
- The machine forms bags automatically from a tubular film of EVA.
- Heat sealing with temperature control.
- Automatic printing of an identification label (barcode, logo, descriptions…) on the bag through thermal transfer graphic printer, in order to ensure the traceability of the recipe at any time.
- Automatic insertion of the bags into the holder containers.
- Containers are moved into the dosing area.
02
Dosing phase
- The bag containers pass under each silos/big bag in a loop process. All the recipe components will be dosed simultaneously.
- Our computer analyzes continuously the position of every container. If the container (according to the recipe) is under the right silo/big bag the dosing cycle is achieved. During this phase a vacuum system will collect any eventual dust that is created by the weighing operation.
- For some difficult and compacted products the system will be equipped with bridge breakers and vibrators. In any case, we can handle any type of chemical product.
- Before the dosing phase the system launches an auto-certification on the weighing scale. The weight that the scale received must correspond to the initial tare and to all dosing cycles when they occur. In this way we can guarantee always the system accuracy.
03
Discharge of the bag
To the end of dosing the bag will be automatically:
- Extracted from the containers.
- Extracted from the internal air.
- Sealed (head sail).
- Final Weigh control on motorized carpet.
- Delivered on a second carpet if wrong automatically.
04
Finished bag
The finished bag will be traceable through the barcode printed on the bag, ready to be delivered into customer’s mixer.
Automatic bags delivery system to customer's mixers
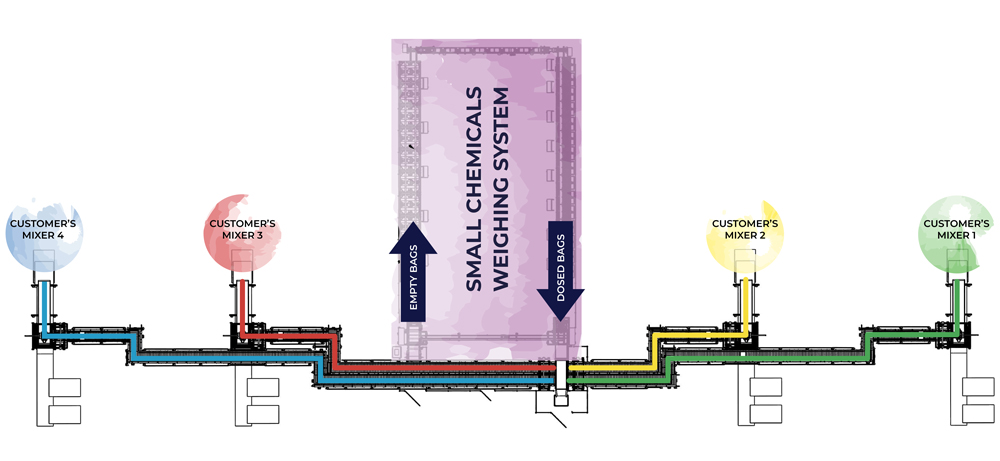
The box containing the dosed bags coming from the small chemicals weighing system will be automatically delivered directly into customer’s mixer. Through transportation lines (automated robot or roller conveyor) the dosing system is connected directly to customer’s mixer, avoiding human intervention during the process.
The operation is completely driven by Color Service management, directly interfaced with mixers.
Let’s see the delivery process:
01
The bag will be placed into the box by the motorized belt.
02
Every corner on the Conveyor is equipped with a Pneumatic Pushing Device.
03
It receives the boxes from the distributor and it provides to pick them up and then turn them upside – down.
04
The distributor lets the bag fall down to the conveyor motorized belt. Finally, it will give the box to the elevator.